China's aviation manufacturing industry is in a period of rapid development, so it is very much looking forward to the further development of industrial robot technology. Under the background of China's vigorous development of aviation technology, industrial robots will certainly play a greater role in aviation manufacturing. Smart hurricane hits industrial robots to promote aviation manufacturing to a new splendor With the gradual deepening of the application of industrial robots in aerospace manufacturing, some deficiencies have begun to emerge, such as low automation degree of job planning and interference collision detection, positioning calibration and offline programming. The long production and preparation time, lack of flexibility and expandability of the equipment lead to low equipment utilization, and the advantages of the robot are sometimes not reflected in the small batch production model of aerospace products. Therefore, future industrial robots in aerospace manufacturing need to be better adapted to the changing task requirements in single-piece and small-batch production modes, complex site environments, improve positioning and movement accuracy, shorten off-line programming and production preparation time, and improve equipment utilization. Rate and so on, really play out the advantages and characteristics of the robot. The following technologies will become common key enabling technologies. High-precision measurement and positioning technology Industrial robots have high repetitive positioning accuracy and low absolute positioning accuracy, and can not meet the requirements of absolute positioning accuracy in digital assembly of aircraft. Therefore, high-precision measurement equipment is required to guide the robot end-effector to achieve servo control of the movement trajectory. At present, large-scale measurements mainly use laser trackers and iGPS. Monocular vision, binocular vision, hand-eye vision, and laser distance sensors all have their own strengths in local measurement. In some special cases, acoustic sensation, Force sensors are also useful. It can be foreseen that multi-sensor information fusion technology will surely be further developed. End-accuracy compensation technology The end-accuracy of a robot is affected by various factors such as kinematic interpolation, robot load, stiffness, mechanical clearance, tool wear, thermal effects, etc. Therefore, in addition to using high-precision measurement instruments, a positioning error model and compensation algorithm are also established. Improve the positioning accuracy of the important means. For this reason, it is necessary to perform parameter identification on the joint stiffness, position error, and temperature-induced deformation of the robot to obtain an error model or an error matrix, and then to provide servo correction to the end effector positioning by the accuracy compensation algorithm. Intelligent planning technology robot is the carrier of automation. Whether it is drilling, spraying, welding, cutting, assembly, gluing, or dispensing, it all depends on the end of the robot to complete the operation strictly according to the predetermined trajectory. Therefore, the result of the trajectory planning directly affects the robot. Work efficiency and efficiency, while the efficiency and automation of trajectory planning directly affect production preparation time. On the basis of deep understanding of the process, automatic path planning, robot trajectory optimization, automatic interference check, process parameters and process optimization are important research directions. In order to improve the intelligence of robots, artificial intelligence methods such as expert systems, fuzzy systems, evolutionary computations, group computing, machine learning, and neural networks will be introduced in large numbers, and techniques such as image recognition, speech recognition, speech synthesis, and natural language understanding It will also be widely used to increase and improve human-computer interaction. In addition, the rapid development of technologies such as cloud computing and big data, resource sharing, knowledge sharing, and data mining provide new ideas for improving robots' analysis, decision-making, and collaboration capabilities. Robot control technology Because industrial robots are a nonlinear, multivariable control object, combined with information feedback on position, moment, force, vision, etc., flexible control, force-forced hybrid control, visual servo control and other methods have been widely used and studied. For high-speed, high-precision, heavy-load operation requirements, the robot control method will still be the focus of research. 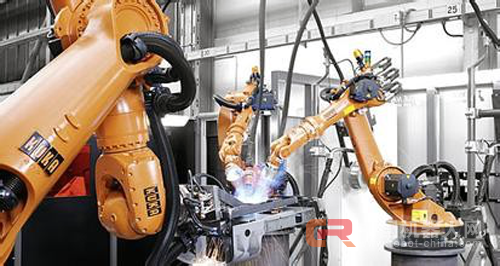
The innovative design of the robot body structure Due to the particularity of the aerospace product structure, the traditional industrial robots sometimes cannot meet the demand. With the gradual deepening of the robotics technology in the aviation manufacturing field, the demand for specialized, special and non-standard robots is increasing. It means that the ontology structure needs to be designed for specific tasks and the application of the robot is expanded. Reconfigurable Flexible Machining Unit Technology In the manufacture and assembly of aircraft, the number of fixtures, the large size, and the variety of fixtures are a large expense. The tooling of the future will adopt a modular design and change the tooling pattern by moving various dynamic modules to adapt to different sizes and types of products. The "No Frame Digital Assembly Technology Center" being developed by Airbus is the product of this concept. The center is a combination of hardware and software assembly workstations that incorporates integrated digital tooling and various assembly, adjustment, and inspection technologies. Can greatly improve the efficiency of aircraft assembly. Digital manufacturing system support technology The digital process design and product manufacturing model based on Model-based Defi- nition (MBD) is derived from the three-dimensional design digital model. The three-dimensional process digital model, tooling digital model, and inspection digital model As a basis for robot job planning and off-line programming, job planning based on 3D digital models, visualization of assembly processes based on lightweight models, digital detection based on MBD, and integrated data management functions based on MBD are indispensable. In addition, future off-line robot programming and control systems need to be more open, including supporting standard 3D data formats, providing standardized data access interfaces, and interconnecting with manufacturing information systems. With the breakthrough and progress of these key technologies, the future of aerospace manufacturing robots will be developed in the direction of intelligence, flexibility, dexterity, and collaboration to adapt to the ever-changing development and new emerging demands of the aviation industry: (1) Intelligent. Existing industrial robots require manual teaching or off-line programming to perform jobs. It is an important development direction of future industrial robots to improve the intelligence of positioning calibration, job planning and collision detection to shorten production preparation time. People even hope that future robots can plan and control their own actions in real time and complete their work independently and autonomously. Instead of being limited to action repetition. (2) Flexibility. Traditional industrial robots pursue speed and accuracy. They are large in weight, large in size, large in power consumption, and rigid, but in some special occasions, lightweight robots with joint force feedback capabilities and joint flexibility are low in weight due to their low weight. , higher load / weight ratio and with flexible control capabilities and other features more advantages. (3) dexterity. Aviation manufacturing often requires operations within complex, hidden product spaces, such as interior monitoring of aircraft panels, fastening and sealing of standard parts, and measurement, installation, painting, inspection of intake ducts, etc., and joint redundancy degrees of freedom. Robots have good prospects due to their large working space and high flexibility. In terms of the walking mechanism, most industrial robots use a track structure, occupying a large amount of work space and the ground, and high plant input and maintenance costs. It is a more economical way to install industrial robots on wheeled or tracked mobile platforms to achieve the purpose of moving around the parts. It is also worth noting that crawling robots that use a vacuum adsorption device to achieve attachment of the workpiece surface are also worthy of attention. (4) Cooperation. Arms or multi-arm robots have attracted more and more attention from many research institutes at home and abroad. Internationally renowned robot manufacturers such as abb, kuka, and YASKAWA have carried out research and development of related products. At present, there are already dual-arm coordination robots for aerospace composite materials. Automatically laid out reports. In addition, although the development of robotics technology is changing with each passing day, it is impossible to completely replace people after all. Robots are integrated into production. Robots work side by side with people to eliminate man-machine isolation and free people from simple and boring work. , Further engaging in more value-added work has always been the most ideal and attractive aerospace manufacturing model in people's minds. At the end of 2012, Germany, Austria, Spain and other countries jointly initiated the VALERI program under the funding of the “Future Factory†project of the 7th Framework Program of the EU. Its purpose is to achieve advanced robot recognition and human-robot cooperative operation. Airbus has also made a bold attempt in FUTURASSY's future project for aircraft assembly. The human-armed dual-arm robot developed by Japan Kawada Industrial Co., Ltd. is applied to the A380 rudder assembly workstation and is riveted together with ordinary human employees. Concluding remarks China's aviation manufacturing industry is in a period of rapid development. The constant emergence of new materials and new processes and the demand for high quality, low cost, and flexible manufacturing have made it urgent for companies to upgrade their technology and equipment. Therefore, we look forward to the further development of industrial robot technology. At the same time, advances in robotics and basic theoretical research have provided opportunities for industrial robots to gain favor in aviation manufacturing. It is foreseeable that under the background of China's vigorous development of aviation technology, industrial robots will surely play a greater role in aviation manufacturing.
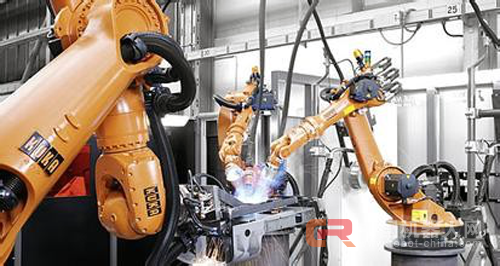
The innovative design of the robot body structure Due to the particularity of the aerospace product structure, the traditional industrial robots sometimes cannot meet the demand. With the gradual deepening of the robotics technology in the aviation manufacturing field, the demand for specialized, special and non-standard robots is increasing. It means that the ontology structure needs to be designed for specific tasks and the application of the robot is expanded. Reconfigurable Flexible Machining Unit Technology In the manufacture and assembly of aircraft, the number of fixtures, the large size, and the variety of fixtures are a large expense. The tooling of the future will adopt a modular design and change the tooling pattern by moving various dynamic modules to adapt to different sizes and types of products. The "No Frame Digital Assembly Technology Center" being developed by Airbus is the product of this concept. The center is a combination of hardware and software assembly workstations that incorporates integrated digital tooling and various assembly, adjustment, and inspection technologies. Can greatly improve the efficiency of aircraft assembly. Digital manufacturing system support technology The digital process design and product manufacturing model based on Model-based Defi- nition (MBD) is derived from the three-dimensional design digital model. The three-dimensional process digital model, tooling digital model, and inspection digital model As a basis for robot job planning and off-line programming, job planning based on 3D digital models, visualization of assembly processes based on lightweight models, digital detection based on MBD, and integrated data management functions based on MBD are indispensable. In addition, future off-line robot programming and control systems need to be more open, including supporting standard 3D data formats, providing standardized data access interfaces, and interconnecting with manufacturing information systems. With the breakthrough and progress of these key technologies, the future of aerospace manufacturing robots will be developed in the direction of intelligence, flexibility, dexterity, and collaboration to adapt to the ever-changing development and new emerging demands of the aviation industry: (1) Intelligent. Existing industrial robots require manual teaching or off-line programming to perform jobs. It is an important development direction of future industrial robots to improve the intelligence of positioning calibration, job planning and collision detection to shorten production preparation time. People even hope that future robots can plan and control their own actions in real time and complete their work independently and autonomously. Instead of being limited to action repetition. (2) Flexibility. Traditional industrial robots pursue speed and accuracy. They are large in weight, large in size, large in power consumption, and rigid, but in some special occasions, lightweight robots with joint force feedback capabilities and joint flexibility are low in weight due to their low weight. , higher load / weight ratio and with flexible control capabilities and other features more advantages. (3) dexterity. Aviation manufacturing often requires operations within complex, hidden product spaces, such as interior monitoring of aircraft panels, fastening and sealing of standard parts, and measurement, installation, painting, inspection of intake ducts, etc., and joint redundancy degrees of freedom. Robots have good prospects due to their large working space and high flexibility. In terms of the walking mechanism, most industrial robots use a track structure, occupying a large amount of work space and the ground, and high plant input and maintenance costs. It is a more economical way to install industrial robots on wheeled or tracked mobile platforms to achieve the purpose of moving around the parts. It is also worth noting that crawling robots that use a vacuum adsorption device to achieve attachment of the workpiece surface are also worthy of attention. (4) Cooperation. Arms or multi-arm robots have attracted more and more attention from many research institutes at home and abroad. Internationally renowned robot manufacturers such as abb, kuka, and YASKAWA have carried out research and development of related products. At present, there are already dual-arm coordination robots for aerospace composite materials. Automatically laid out reports. In addition, although the development of robotics technology is changing with each passing day, it is impossible to completely replace people after all. Robots are integrated into production. Robots work side by side with people to eliminate man-machine isolation and free people from simple and boring work. , Further engaging in more value-added work has always been the most ideal and attractive aerospace manufacturing model in people's minds. At the end of 2012, Germany, Austria, Spain and other countries jointly initiated the VALERI program under the funding of the “Future Factory†project of the 7th Framework Program of the EU. Its purpose is to achieve advanced robot recognition and human-robot cooperative operation. Airbus has also made a bold attempt in FUTURASSY's future project for aircraft assembly. The human-armed dual-arm robot developed by Japan Kawada Industrial Co., Ltd. is applied to the A380 rudder assembly workstation and is riveted together with ordinary human employees. Concluding remarks China's aviation manufacturing industry is in a period of rapid development. The constant emergence of new materials and new processes and the demand for high quality, low cost, and flexible manufacturing have made it urgent for companies to upgrade their technology and equipment. Therefore, we look forward to the further development of industrial robot technology. At the same time, advances in robotics and basic theoretical research have provided opportunities for industrial robots to gain favor in aviation manufacturing. It is foreseeable that under the background of China's vigorous development of aviation technology, industrial robots will surely play a greater role in aviation manufacturing.
Digit Segment Led Display,Washing Machine Display,Smd Led Display,Bar Segment Led Display
Wuxi Ark Technology Electronic Co.,Ltd. , https://www.arkledcn.com